Case Study: CMI Hino
Overview of client
CMI Hino, a provider of heavy vehicle service and maintenance, operates multiple sites across Melbourne to offer comprehensive geographic coverage for their clients. As part of their growth, CMI Hino expanded into a new leased facility in Campbellfield, which houses a large maintenance workshop and a showroom. However, the new site presented a challenge: it lacked a compliant wash bay necessary for post-service vehicle cleaning, and the lease agreement restricted any extensive modifications or civil works.
The Solution
CleanaWater provided CMI Hino with a comprehensive turnkey solution, offering a modular wash bay tailored to their needs. The 6.5m by 12m wash bay was designed with three-sided walls, extended to a height of 2.4m to protect the surrounding area, and included five ramps for easy access. One of the key benefits of CleanaWater’s modular design was that no civil works were required, preserving the integrity of the existing concrete floor and ensuring full compliance with the lease terms.
The wash bay features an electric diesel-heated high-pressure cleaning system with self-retracting hose reel, as well as detergent injection capabilities for effective cleaning. Additionally, a sludge settling tank was integrated into the oil water separator design, allowing for extended service intervals and cost savings. CleanaWater also managed the entire project, including plumbing, electrical works, and securing a trade waste agreement with Yarra Valley Water. CMI Hino simply needed to specify the desired location for the wash bay, and CleanaWater handled the rest.
The Results
CMI Hino’s operations manager praised the new wash bay, stating it was “the best wash bay we’ve ever used.” The solution not only met their current requirements but also offered the flexibility for future relocation, making it ideal for their leased facility.
CMI Hino is highly satisfied with CleanaWater’s solution and recommends the modular wash bay for its adaptability, cost-effectiveness, and compliance with lease agreements.
After-sales support
Comprehensive after-sales service. Seven days a week. That's the CleanaWater support promise.
We have industry experts located in Melbourne, Brisbane, and Newcastle. So you can always speak to somebody who understands your local market.
They're available around the clock to answer any queries you may have – whether it's about our systems or odour and water treatment in general.
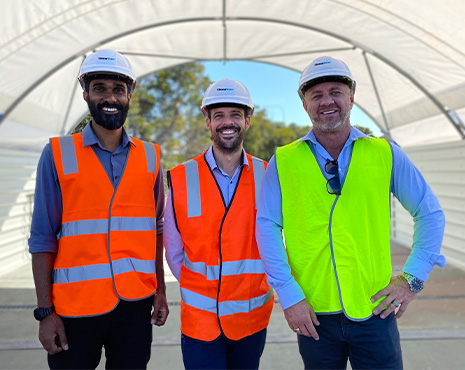
Cleanawater's end-to-end process
Step 1
Process Development
CleanaWater's project engineers confirm all site parameters, commence design and process evaluations on specific requirements for your waste water treatment plant works.
Step 2
Conceptual Modelling
Conceptual 3D models, predictive flow and performance analysis models are tested prior to manufacturing a site's waste treatment system.
Step 3
Manufacturing
We update the design briefs and create build drawings before manufacturing and commissioning at our Melbourne facility.
Step 4
Installation
The CleanaWater team complete water waste management installation and commissioning on site – without disrupting your operations.
Contact us
Our locations
Newcastle
Mayfield West
NSW 2304
Melbourne
Thomastown
VIC 3074
Brisbane
Geebung
QLD 4034
Perth
Osborne Park
WA 6017
Adelaide
Wayville
SA 5034